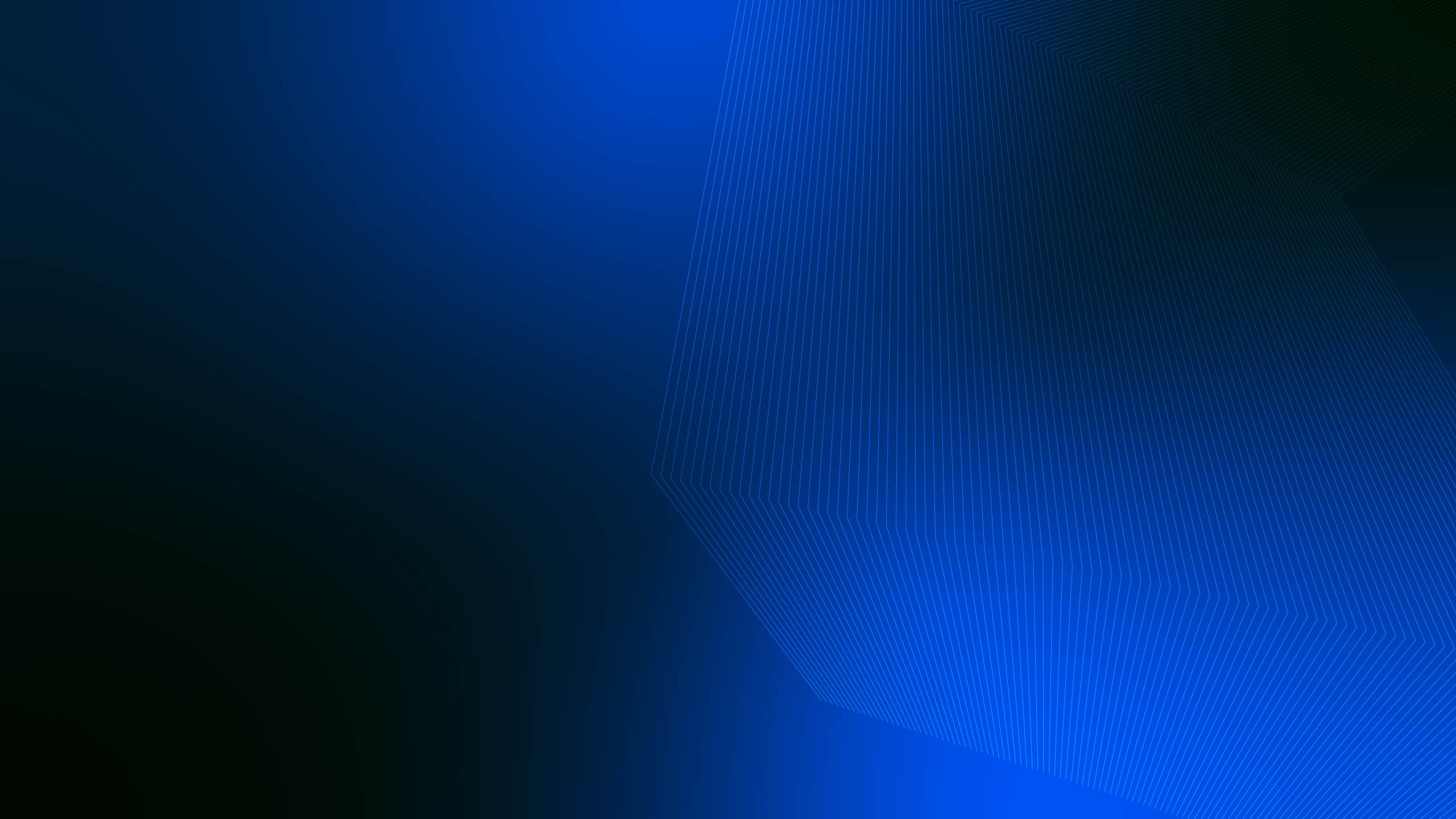
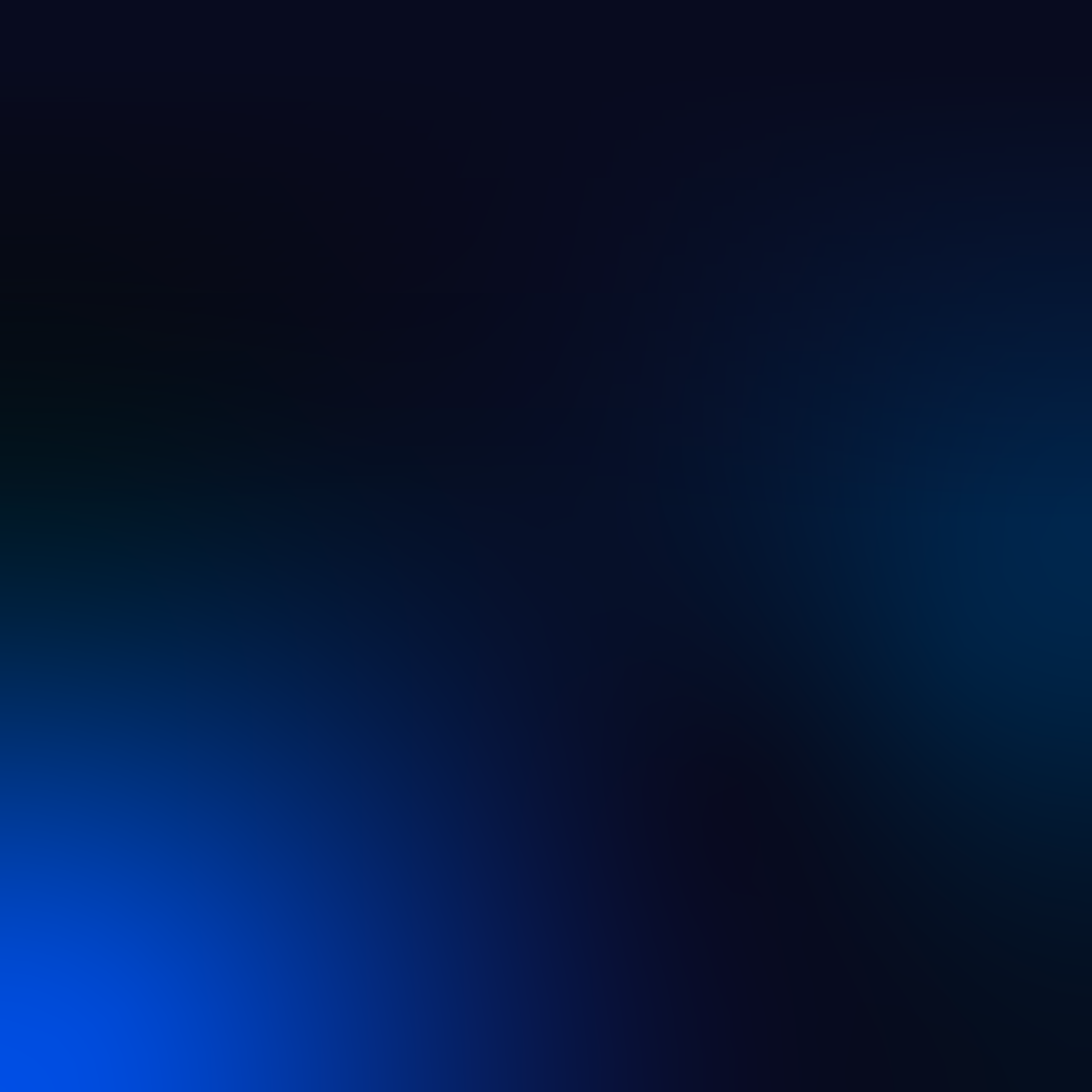
Recharge Industries™ uses a unique patented chemistry known as bio-mineralized lithium mixed-metal phosphate (BM-LMP) to create battery cells.
This chemistry results in fewer metals and less-toxic materials than comparable lithium cell batteries, making them safer and more environmentally-friendly.
BM-LMP
BM-LMP stands for Bio-Mineralized Lithium Mixed-Metal Phosphate. While Recharge Industries™ cannot disclose the exact metals in the battery chemistry, it primarily uses manganese and iron.
The technology is a phosphate-based composite cathode that utilizes low-cost materials, molecular doping of lithium-rich bio-mineral in the super-cell crystal structure. The battery technology contains no cobalt or nickel.
Technology Partner: Charge C4V
Our U.S. technology partner C4V, leverages its expertise in electrode design and process development to create next-generation storage materials that can be seamlessly integrated into current battery cell manufacturing lines. This allows for continuous upgrades to the facility without requiring significant infrastructure changes.
Recharge Industries™ has obtained exclusive rights to the technology and battery cell patented chemistry, manufacturing process and technical product designs as well as C4V’s qualified supply chain.
The technology used by Recharge Industries™ was developed under the guidance and mentorship of Professor M. Stanley Whittingham, Nobel Laureate for Chemistry, who is recognized as the “father of the lithium-ion battery”.

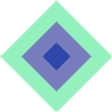
Safety
Batteries awarded high safety from the New York City Fire Department.
Minimal risk of thermal runaway for cells.
Low toxic profile, no toxic fumes or leaks.
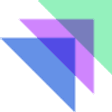
Performance
High energy density >200Wh/kg
Superior cycle count compared to competing technologies >8000
Demonstrated 85% charge of Li-ion battery in 10 minutes
100+ patents in 30+ countries
Highest voltage on the market
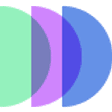
Reliability
Demonstration cells are made with commercial process, fully transferable to giga-facilities
Rigorously tested and qualified supply chain
Strict traceability of raw materials up to mine
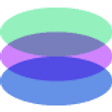
Cost
20% lower cost compared to NMC and NCA technologies
“No-Cobalt” lowers the bill of materials and operating costs of Gen 1 battery
Battery manufacturing leverages cutting-edge digital technologies
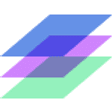
Environment
Primary energy consumption associated with the cathode active materials is a strong driver of the Li-ion battery’s environmental impact.
Recharge Industries™ cells use fewer metals and less-toxic materials than comparable lithium cell batteries.
Recharge Industries™ cells then lead to lower global warming, acidification, smog, and energy consumption when compared to other Li-ion battery production processes – New York Research & Development Authority (NYSERDA) independent commissioned report
NYSERDA Validation
The battery cell chemistry, licensed exclusively to Recharge Industries™ by C4V, has been extensively researched by the New York State Energy Research and Development Authority in a lifecycle assessment.
The report, titled Life Cycle Assessment: C4VLithium-Ion Battery Cells for Electric Vehicles, was completed in October 2019 and found that the type of battery cells, “use fewer metals and less-toxic materials than comparable modelled lithium cell batteries with higher impacts.”
Department of Defense Validation
Technology validated by US Department of Defense research teams.
The technology and battery cells which Recharge Industries™ holds exclusive rights to has been validated by the US Department of Defense (ARL and C5ISR).